Management Reserve Best Practice Tips
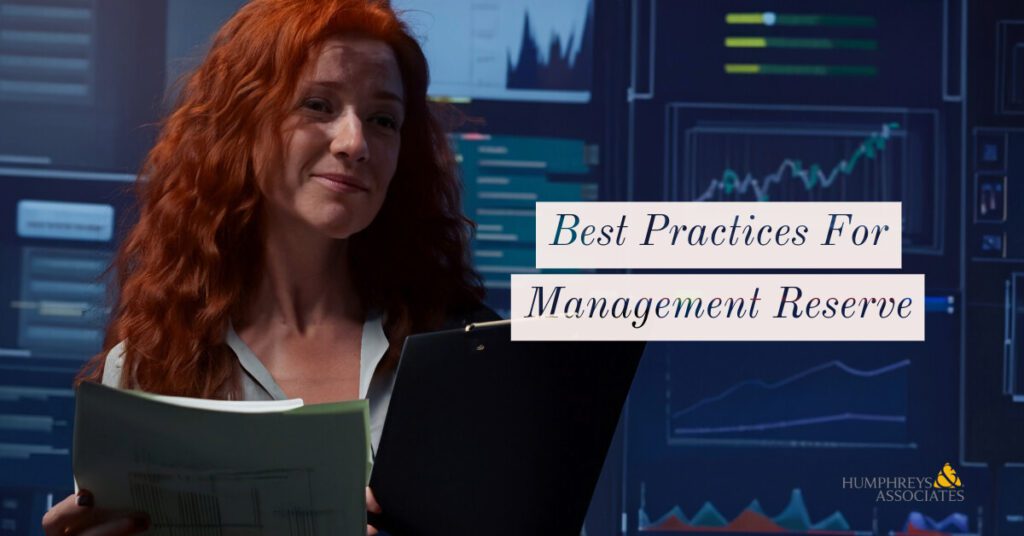
A recurring theme H&A earned value consultants find themselves discussing with clients is emphasizing that management reserve (MR) is a very precious budget set aside that must be protected and used appropriately. Unfortunately, MR is often used inappropriately, and quickly depleted in the early stages of a project.
What happens when MR is consumed for other uses than what it was intended? There is no budget available for appropriate uses of MR such as for emerging work, rework, redesign, or make/buy adjustments within the scope of the contract when it is needed in the latter stages of a project. When that happens, a project manager is forced to create a “home” for actual costs for these activities. This results in other inadvisable actions such as:
- Zero budget work packages which are also known as estimate to complete (ETC) only work packages.
- De earning the budgeted cost for work performed (BCWP) and opening completed work packages to accept charges.
- Culling budgets from future unopened work packages, and if they exist, planning packages, summary level planning packages (SLPP), and undistributed budget (UB).
These actions will call into question the integrity of the EVMS and EVM data. The customer conducting EVMS surveillance will also be quick to point out this deficiency in the EVMS implementation and raise the issue to ensure it has management’s attention to correct. The inappropriate use of MR has created a cascade of problems that could have been avoided. In some instances, project personnel were simply not following the rules for the use of MR found in the contractor’s EVM System Description. That’s an easier problem to resolve than other root causes.
The Role of Risk and Opportunity Management in Establishing MR
What H&A earned value consultants often uncover as the root cause of inappropriate uses of MR was that a robust risk and opportunity (R&O) management process would have made a difference in establishing a quantified set aside for MR to handle realized risks. Proactively identifying and managing risks improves project performance. The expectation of specific risks occurring leads to risk handling plans that lower the likelihood and impact of risks. It also provides an informed basis to establish an adequate amount of MR that reflects identified and assessed risks.
The risk assessment provides additional information that assists a project manager’s decision making process to validate a request to use MR is appropriate and has the backup data needed to justify the use of MR and the amount of MR allocated. This detail is necessary for the baseline change request (BCR) approval process as well as the Integrated Program Management Report (IPMR) Format 5 or Integrated Program Management Data and Analysis Report (IPMDAR) Performance Narrative Report (PNR). A project manager is required to identify the changes to MR during the reporting period and provide a brief explanation of the change. This explanation has the potential to pique the interest of the customer to gain a better understanding of why MR was used and the potential impact to the integrity of the EVM data.
Note: MR may increase or decrease for a variety of reasons. The primary use of MR is to handle realized risks within a control account that is within the statement of work (SOW) for the contract. All MR debits or credits should be tracked in a log for full traceability for the entire life of the project. Remember that MR can never be a negative value.
Acceptable Uses of MR
As highlighted in an H&A article titled “The Effective Use of Management Reserve,” examples of the appropriate uses of MR include:
- Newly identified work is authorized and assigned to a control account manager (CAM). It may be that once the work begins, one or more tasks that were missed in the original planning process now need to be scheduled and resource loaded. Newly identified work could also be the result of internal replanning that required a change in approach or resource requirements.
An example of this could be a project manager issued a work authorization to a CAM to conduct three tests to meet the requirements in the contract SOW. In the middle of the first test, it becomes clear to the CAM and project manager that a fourth test will be necessary. The project manager and CAM should be aware of this potential risk and be prepared to implement their risk handling strategy as a result of the R&O management process. The CAM can quickly prepare a BCR that the project manager can immediately approve to allocate MR budget to complete the fourth test.
- It is necessary to redo a task. This may include unanticipated redesign, remake, or retest. Hopefully, the project’s risk register identified the potential risks associated with the original tasks and management was prepared for the realized risk.
- Make/buy adjustments. This could result in an MR debit or credit.
- Statement of work transfers from one organization to another. This could result in an MR debit or credit.
Inadvisable Uses of MR Commonly Allowed
Although it is often allowed in a contractor’s EVM System Description, it is inadvisable to use MR for direct and indirect rate changes in the future. Note: MR should never be used to make any rate adjustments (or any other adjustments) to historical budgeted cost for work scheduled (BCWS) or BCWP data.
A rate change is not a change to the SOW for a CAM. It is merely a change to the cost of that work. Cost variances that occur because of direct and/or indirect rate changes can easily be explained in a Variance Analysis Report (VAR). Ironically, this use of MR is typically treated as a one-way street. Contractors apply MR when the direct and/or indirect rates are going up in the future but do not return to MR when the rates are projected to go down.
When a contractor’s EVM System Description allows MR to be used for future direct and/or indirect rate changes, ideally, the likely rate changes are identified as a risk and quantified when the initial MR is established for a project. This requirement should be noted in the EVM System Description. That way the set aside for MR includes budget for corporate rate adjustments that are outside of the control of the project manager or CAM.
Another example of a commonly allowed but inadvisable use of MR is to “true up” a purchase order that is in excess of the original budget at completion (BAC) for material, equipment, or purchased services. For example, a project manager issues a work authorization to a CAM that includes purchasing material, equipment, or services from a supplier. The CAM then reaches an agreement with a supplier with scope, schedule, and budget. If that agreement is greater or less than the BAC, MR should not be applied, nor should budget be returned to MR to make the BAC match the PO value. Assuming the scope does not change, then MR should not be used to wipe out a cost variance whether positive or negative. The cost variance can be easily explained and the EAC can be increased or decreased. This is another example where contractors are treating this as a one-way street; they apply MR when it goes up, but do not return to MR when it goes down. A contractor would not “true up” for internal work overruns/underruns so why “true-up” for material or services provided by a supplier?
Best Practice Tips
The following is a short list of best practices H&A earned value consultants often recommend clients implement for managing MR.
- The EVM System Description should clearly spell out what are appropriate and inappropriate uses of MR. It should also provide guidance to eliminate instances of the “one way street” debit from MR. If needed, provide supplemental procedures, decision trees, or other work instructions to help project personnel follow EVM best practices and preserve MR for handling realized risks which typically occur in latter stages of a project.
- Ensure that the R&O management process is integrated with the EVMS and provides the necessary risk identification and assessment information for the project manager to establish a realistic MR set aside based on quantifiable information. Where applicable, ensure likely rate changes are captured as a potential risk to the project and considered when the initial MR for the project is established if they intend to use MR for rate changes in the future.
- Conduct recurring training to reinforce the purpose for MR and the appropriate use of MR. A recommended approach is to discuss a variety of use cases with project personnel so they know how to handle various situations that may occur on a project.
Have you noticed “creative” uses of MR that are contrary to EVM best practices? Hopefully, you identified those situations as part of your EVMS self-governance process and were able to quickly implement corrective actions before your customer pointed out the issue to you. H&A earned value consultants often assist clients with producing procedures or work instructions that clearly spell out how to use MR appropriately. We also offer a range of EVMS training to reinforce EVM best practices including the appropriate use of MR. Call us today to get started.
Management Reserve Best Practice Tips Read Post »