Introduction to Earned Value Management Systems (EVMS)
We are starting a new series that will share some of the adapted video content from our EVMS Workshops. This first video is a brief overview of Earned Value Management, what it is, where it came from, and why it was developed.
More EVMS Training
If you liked this video you can purchase the entire course below. This video is an excerpt from the Department of Defense (DOD) version of this eLearning module. We also offer the same course customized for the Department of Energy’s (DOE) specific Earned Value Management (EVM) implementation/requirements, as well as a version of the course customized for NASA’s EVM implementation/requirements.
— Purchase This Course —
EVMS DOD Virtual Learning Lab
— Purchase the DOE Version of this Course —
EVMS DOE Virtual Learning Lab
— Purchase the NASA Version —
EVMS NASA Virtual Learning Lab
EVMS Document Matrix
Not sure what the different requirements are between the DOE and NASA? Can’t remember if Cost and Software Data Reporting (CSDR) is required for an NSA contract? Check out our easy to read Earned Value Management Systems Document Matrix
All Online Courses
All Online Courses Available from Humphreys & Associates
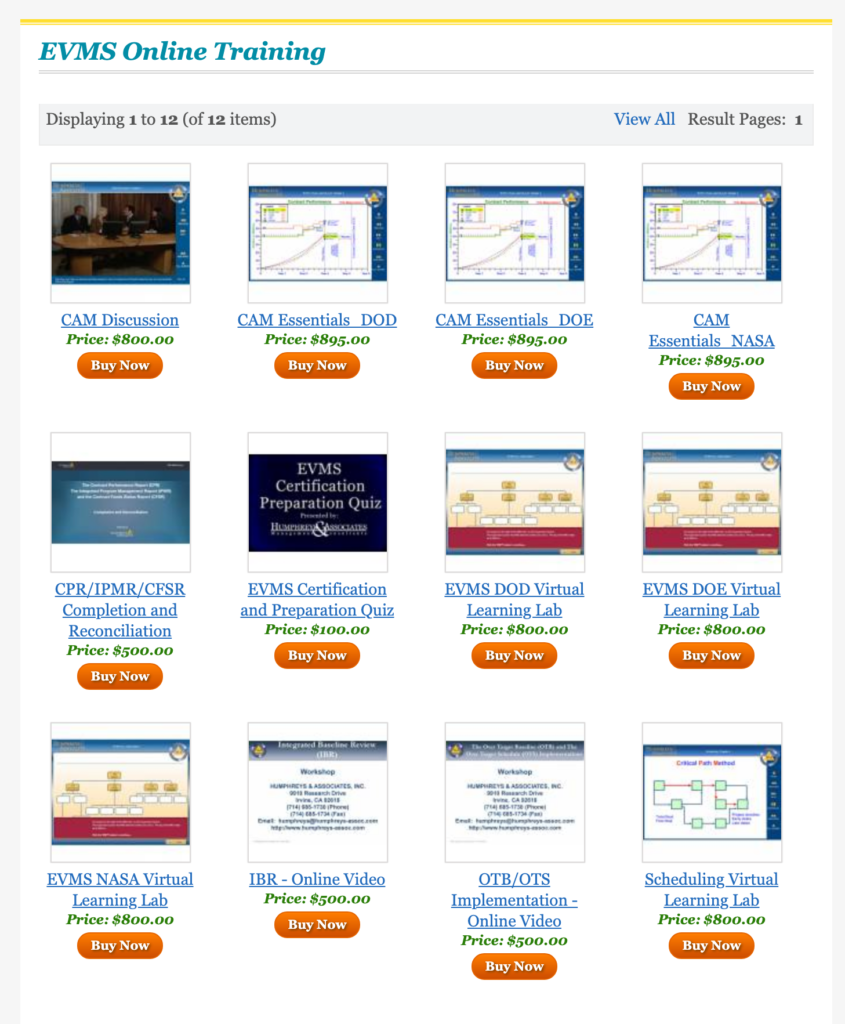
Other Posts in this Series
Introduction to Earned Value Management Systems (EVMS) Read Post »