How to Get the Most from Your IMS: What Makes an IMS Useful?
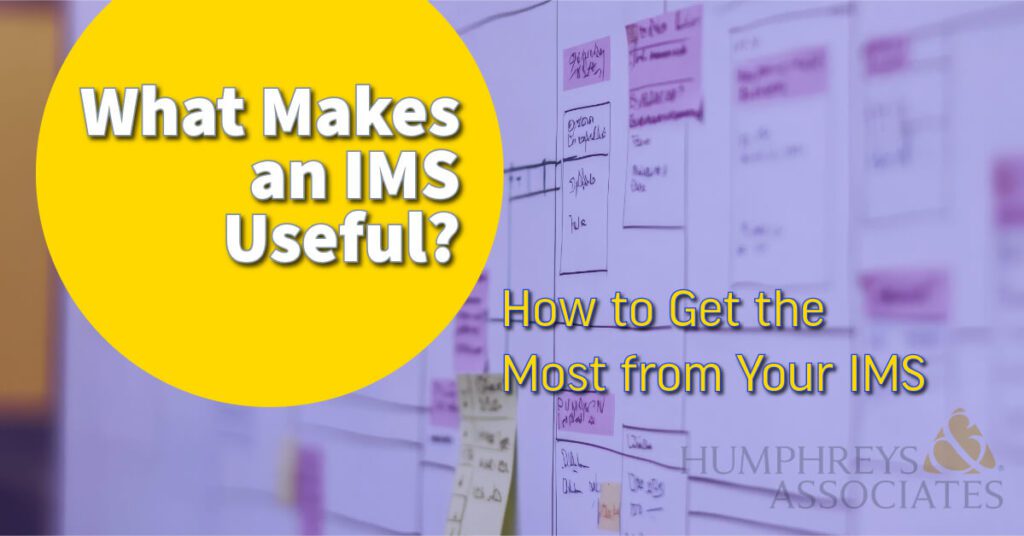
A major challenge with an Integrated Master Scheule (IMS) is making the most out of this powerful project management tool. Large and even not-so-large projects are required to have an IMS which adheres to the requirements of the Integrated Program Management Report (IPMR) or Integrated Program Management Data and Analysis Report (IPMDAR) Data Item Description (DID) and meets the schedule data quality checks available. But having met the DID requirements and passing the quality checks does not mean the IMS is being used to get the most information into the hands of decision makers on the project.
The IPMR or IPMDAR DID, even though detailed and thorough, is generic. The same DID is used on a contract whether it is for an important new hardware-based system, a new software system, or some other goal. The DID misses the point that the type of product on the contract means that unique topics may be the most important. There is no focus in the DID; it is high level and comprehensive. What’s missing are the special interest or special focus schedules that can be drawn from the IMS with good coding, grouping, filtering, and sorting techniques.
Remember that the statement of work (SOW) for the project is really comprised of promises made in the various plans submitted in the proposal and updated after contract award. The System Engineering Management Plan (SEMP), the Software Development Plan (SDP), Make/Buy Plan, Procurement Plan, Test and Evaluation Management Plan (TEMP), and others all contain commitments that should be translated into actions in the IMS. There should be access to the portions of the IMS that show how these commitments will be accomplished.
Examples of Special Interest Schedules
On a new hardware-based project, key pieces of information revolve around getting designs done and into a form to plan for the procurement of the various things needed to build the end items. This information often resides in the IMS but must be pulled out into a “drawing release” schedule. That is a schedule showing the transition from design to 3-D models or drawings. Pinpointing the times and links in the IMS where design becomes actionable for procurement enables the project team and their suppliers to be prepared to execute the procurements. The teams or engineers (designers) and procurement people should be focused on the drawing release schedule with frequent, at least weekly meetings to coordinate.
One of the serious issues I witnessed on a project was the lack of preparedness in having trained and qualified drawing checkers who could sign-off and release drawings. Because of the need for flight safety considerations, the drawing checker position could only be filled by qualified people. Instead of preparing months ahead for the wave of drawings, the waves were allowed to crash into the far-too-few checkers. What was supposed to be a short cycle became weeks long as drawings sat waiting for release.
As the transition is made from design to production, then the procurement schedule becomes another focused schedule which should show the information about what is being procured, from whom, and when it will be delivered. This information is used by the engineers, procurement, and inventory control people including receiving to understand the timing and volume of inbound items. Frequent coordination with suppliers and internal team members using this focused schedule helps to ensure a smooth process. Will the factory be ready to receive, inspect, process, and store all the inbound items?
What about software development as a special topic focus schedule? This is often needed. The project personnel must be able to quickly understand where in the cycle the software is and when releases will be made as well as what the release is needed for in the overall project.
Think about all the other important focus areas that could exist on a project. For example, the training effort should be in a focused schedule showing the development of the training material (courseware), training aids, facilities, instructor preparation and anything else needed to execute the statement of work related to training.
Testing is possibly more complicated than training. This includes development of test plans and procedures, as well as the creation of test fixtures and tools. The preparation of test personnel capable of performing complicated tests should be in the focused schedule.
By now you get the idea. The IMS is the combination of all these schedules, the thing that coordinates between and among them. But the focused schedules are the real bread-and-butter of the schedule discipline. It is shocking to see a project where these do not exist. Maybe the managers don’t know they are needed or possibly that they are available. Maybe the schedule team did not prepare for these extractions from the IMS.
If your project does not have focused schedules and does not use them, the project is in jeopardy. These schedules should be generated and used frequently; weekly at least. Even if the IMS itself is only undergoing a monthly update, the detailed schedules should be much more alive and part of the weekly communication between work teams on the project.
Tips and Suggestions
- How to get started. Begin with the source documents and their authors, the SEMP, the TEMP, and so on. Make a list of the likely focused schedules that need to be drawn from the IMS. Read them and extract the information you need to build your IMS. If you are just starting the IMS, you could build individual schedules with the authors and then integrate them into the IMS. If you already have built the IMS, you can find the tasks you need and code them so they will appear on the focused schedule. Once coded, extract the focused schedule from the IMS using the applicable coding filters and verify it matches the commitments that were made in the source documents from the various authors.
- Hold “report court.” Rather than reading and sorting through all the various plans, schedule a project meeting with the key team members and ask them what reports and what schedules they need to do their jobs. Remind them of the commitments they made in the plans. They can bring or provide a list and description to you, and you can decide “in court” which items you can or cannot incorporate into the IMS. That can help to streamline what is included in the IMS and who is responsible for what.
- Create a schedule data dictionary if you haven’t already done so. This is essential to identify standard as well as project unique activity, milestone, or resource coding and how the coding is used so there is a common understanding of the content. The customer will need this information as well as when the IMS is provided as a monthly performance reporting data deliverable (see the IPMDAR Section 2.4.2.20, Data Dictionary for Native Schedule File). It is a prerequisite to ensure consistency in use as well as to establish a level of discipline throughout the IMS development and maintenance process. Ensure tasks always include the necessary coding. Ideally, you did your homework on the likely special topic schedules you need to draw from the IMS before starting to build the IMS. Otherwise you may need to determine various sorting and filter techniques to identify the tasks that require additional coding details. As noted above, once the tasks are coded, you or other project personnel will be able to extract the various special interest schedules from the IMS as needed.
Need help?
Building a useful IMS for complex projects is not easy. Up front planning for the development of the IMS can help to identify the necessary outline codes and other coding to be able to group, filter, or sort the activities to extract the special topic or special focus details from the IMS. The IMS is an essential communication tool for everyone on the project. How the schedule is constructed and coded makes a difference. H&A scheduling subject matter experts (SMEs) have decades of experience in a variety of complex project environments and can help you avoid common pitfalls. Contact us today.
How to Get the Most from Your IMS: What Makes an IMS Useful? Read Post »