Planning and Managing EVM by Elements of Cost (EOC) – Use a New EOC – Part 3
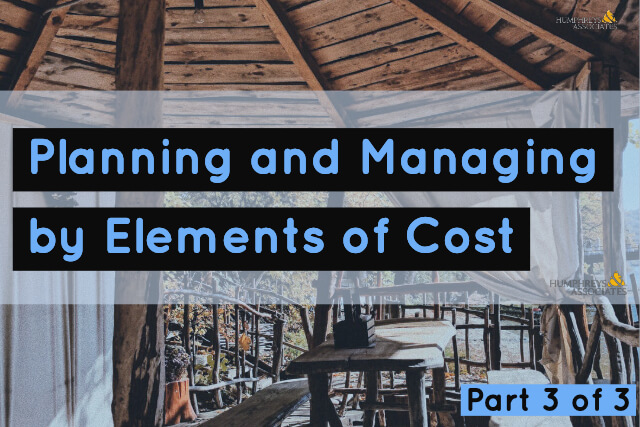
<< Review Part 2
In Part 2 we talked about the over-application of EOCs at or below the Work Package level and how a CAR assuming that a charge against an Element Of Cost (EOC) equals a charge against a “zero-budgeted WP” was inaccurate.
Use a New EOC
Both of the examples from part 2 were over-applications of the EOC requirement. The point here was that the work (it was to design a circuit card), was planned as labor and was also accomplished (earned) in the month it was planned; so the value would be “earned” as planned. In that period, however, it happened that the planned resource was not available, so the work was actually accomplished using a different EOC such as a subcontractor engineer. The contractor’s system properly showed that the design had been completed and the value earned and that the ACWP for that completion was also in the system (i.e. consistent with the BCWP). However, it just happened to be the Subcontract EOC instead of the Labor EOC originally planned, and the CAM addressed the cost difference in the VAR for the Control Account. The team’s comments on the CARs were that the CAM should have replanned the effort using the new EOC instead of the original one. The problem with this is that in many cases the CAM does not know the original resource is not going to be available until the day it happens. There would (1) be no time to process the change and (2) the change would occur in the “freeze period” (actually in the current month), and (3) this could result in unnecessarily large numbers of Change Requests since these types of events commonly occur in the industry.
Noted instances:
- Work planned and earned as internal labor (Labor EOC) had to be performed by contract support (subcontract EOC) in that period because of the non-availability of the planned resource.
- [Some Contractors consider each labor grade a separate EOC within labor] Work planned and earned for an Engineer 2. However, the period the work was performed used an Engineer 3 (higher cost).
- The plan was to build sub-assemblies in-house (Labor EOC), but a machine breakdown necessitated having a vendor provide substitute off-the-shelf assemblies (Material EOC) that month.
In each of these cases, the “EOC ACWP substitution” was temporary, and the work resumed the next period as planned, using the originally planned Element of Cost. The key here is that in each case, the work was performed, and so it was earned; as it should have been. The only difference was that a different EOC was used to accomplish the work – a simple Cost Variance. While it is certainly true that each WP (and PP) should be planned and WPs earned using a single EOC, the misinterpretation here was that every EOC then is a Work package and they are not. In other words, temporarily using a different Engineer category than planned, or using contract support instead of internal labor, or substituting a purchased material item instead of fabricating internally, etc. simply represents a Cost Variances, and should not be cited as a violation of the EVMS Guidelines.
The “consistency” required by the Guideline and the sub-question is that the EOC actually used was expended in the same period in which the work was completed and the Earned Value claimed (i.e. consistent with the BCWP). The variance analysis would show BCWS, BCWP, and ACWP at the CA level with the EOC details at lower levels.
Now for the big “HOWEVER”!
If the switch in use of the alternate EOC is short term, then the differences should be addressed as a Cost Variance (which could be higher or lower than with the planned EOC); HOWEVER, if the change is expected to be permanent or long term, then the CAM should replan the remainder of the work package using the new EOC, and the EAC should be updated, as well, to reflect the new anticipated total cost using that revised EOC.
Note: Some contractors have what is called a “gray badge” environment, whereby a subcontractor charges their labor directly into the Prime contractor’s labor system. Under this arrangement, for this subcontractor, there would be no difference in EOC if the subcontractor performed the work instead of the prime contractor.
Humphreys & Associates is available for consulting and information on this topic. Give us a call!
Planning and Managing EVM by Elements of Cost (EOC) – Use a New EOC – Part 3 Read Post »