Earning Value for Material – The Correct Approach – Part 1
Earning Value for Material
Last Updated May 22, 2025
A common question that H&A earned value consultants are asked is “What is the most common point to claim earned value (the budgeted cost for work performed or BCWP) for material?”
The answer? There is not one point for earning value for all categories of material.
Guideline 21 in the EIA-748-D Standard1 for Earned Value Management Systems (EVMS) says, “…earned value is measured and at the point in time most suitable for the category of material involved…” Notice the text “suitable for the category of material.”
Let’s look at the two most common high-level types of material categories for discussion: 1) Engineering and 2) Manufacturing.
Engineering material earned value (EV) is typically claimed at receipt. Manufacturing material EV is typically claimed when issued from inventory (usage or disbursement). Point of usage is also useful for planning major assemblies in the integrated master schedule (IMS) rather than a myriad of smaller items that would be needed for the assemblies. Planning and earning only the major assemblies as they go to final assembly can simplify the IMS and the EVMS process. Claiming BCWP when material is taken into inventory or at final distribution are also valid options.
The most common acceptable points for claiming earned value for the various material categories are illustrated below.
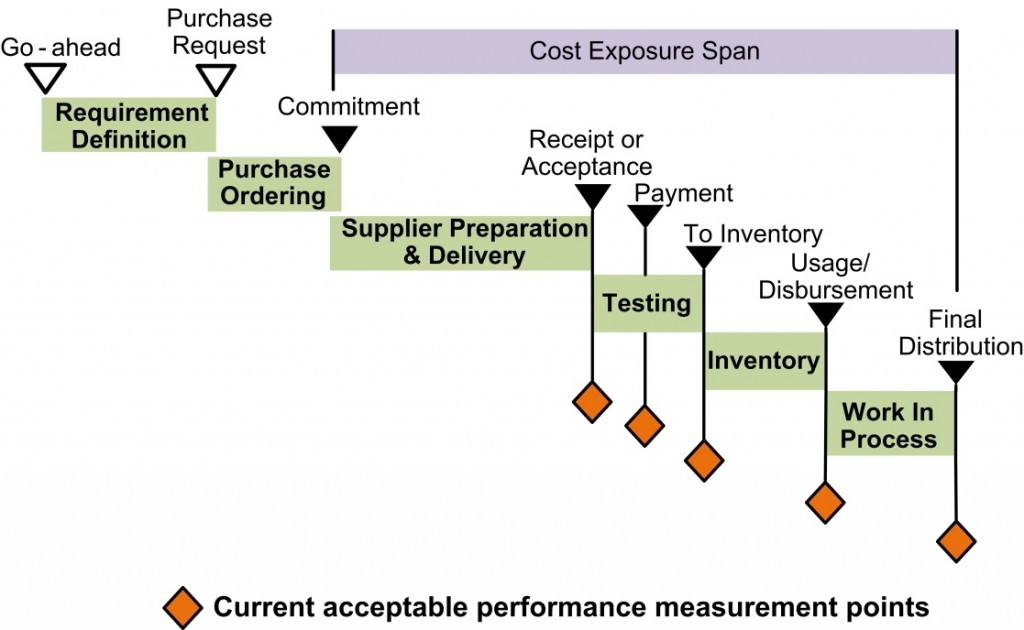
For production programs, based on the completion or delivery dates for end products, the M/ERP system creates a detailed set-back schedule for material required within each build station to achieve completion by the required delivery dates to support “just-in-time” processes. Large production or manufacturing facilities maintain inventories of specific materials to ensure their lines continue in operation.
What happens in some facilities, however, is that contractors have placed the emphasis on the next part of Guideline 21 that says “…but no earlier than the time of actual receipt of material” as their authority to earn value for all material at point of receipt. These contractors are asking for trouble with this misinterpretation. Contractors should base their plans and EV on the category of material involved.
Whenever contractors earn value at the point of receipt for material they plan to maintain in their inventory bins for several months, they open themselves to have DCMA write Deficiency Reports (DRs) or Corrective Action Requests (CARs) for using inappropriate points in time to earn value for material.
- Rationale. When you claim EV, you are telling the customer you are a certain percent complete with the program. For example, if materials represent 70 percent of your contract, earning value for all the material (or a large part of it) up front says (in the performance report to the customer) “I am 70% done with your program.” The customer tends to think in terms of “7 of my 10 airplanes are completed” when in fact none are completed.
- The result? A very unhappy customer because you indicated incorrectly (in the performance report) you are ahead of schedule. This false lead erodes away until you are late delivering the planes, helicopters, ships, tanks, or other contracted items to the customer.
- The take away. A number of contractors are incorrect in thinking they can earn value for all material at the point of receipt. The EIA-748 Guidelines have always required the distinction by material category (there are always more than just the two categories discussed above). DoD and DCMA have always stated there is no one point for claiming material earned value.
Also see these related blogs:
- Earning Value for Material – The Correct Approach – Part 2.
- EVM Material Earned Value – Price vs. Usage Variance Analysis – Part 3.
- Earned Value Management Systems (EVMS) – Residual Material Accountability – Part 4.
- Aligning ACWP with BCWP for EVM | Earned Value Management.
- EVMS compliance: Material Transfers and Loan/Paybacks.
Need help determining the appropriate earned value techniques to use for material? H&A can assist you with clearly defining the requirements for the different categories in your business environment. Contact us today.
- EIA-748-D Guideline 21 content maps to the EIA-748-E Guidelines 14 and 16 which streamlined the content in D Guideline 21. EIA-748-E Guideline 14 states in part: “Earned value for material items may not be credited earlier than the actual receipt of the material nor later than the consumption of the item.” ↩︎
Earning Value for Material – The Correct Approach – Part 1 Read Post »