Earned Value Management (EVM)
Planning and Managing EVM by Elements of Cost (EOC) – Use a New EOC – Part 3
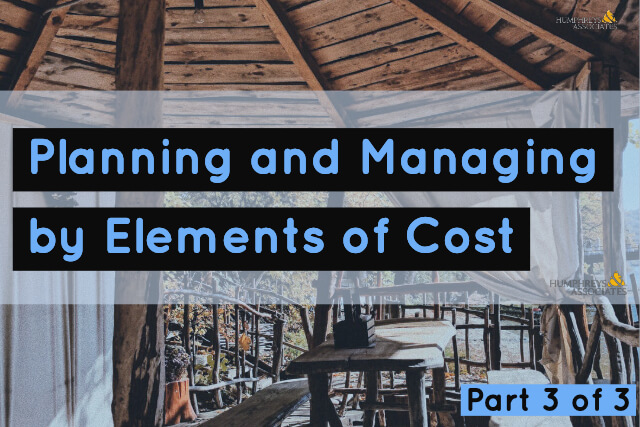
<< Review Part 2
In Part 2 we talked about the over-application of EOCs at or below the Work Package level and how a CAR assuming that a charge against an Element Of Cost (EOC) equals a charge against a “zero-budgeted WP” was inaccurate.
Use a New EOC
Both of the examples from part 2 were over-applications of the EOC requirement. The point here was that the work (it was to design a circuit card), was planned as labor and was also accomplished (earned) in the month it was planned; so the value would be “earned” as planned. In that period, however, it happened that the planned resource was not available, so the work was actually accomplished using a different EOC such as a subcontractor engineer. The contractor’s system properly showed that the design had been completed and the value earned and that the ACWP for that completion was also in the system (i.e. consistent with the BCWP). However, it just happened to be the Subcontract EOC instead of the Labor EOC originally planned, and the CAM addressed the cost difference in the VAR for the Control Account. The team’s comments on the CARs were that the CAM should have replanned the effort using the new EOC instead of the original one. The problem with this is that in many cases the CAM does not know the original resource is not going to be available until the day it happens. There would (1) be no time to process the change and (2) the change would occur in the “freeze period” (actually in the current month), and (3) this could result in unnecessarily large numbers of Change Requests since these types of events commonly occur in the industry.
Noted instances:
- Work planned and earned as internal labor (Labor EOC) had to be performed by contract support (subcontract EOC) in that period because of the non-availability of the planned resource.
- [Some Contractors consider each labor grade a separate EOC within labor] Work planned and earned for an Engineer 2. However, the period the work was performed used an Engineer 3 (higher cost).
- The plan was to build sub-assemblies in-house (Labor EOC), but a machine breakdown necessitated having a vendor provide substitute off-the-shelf assemblies (Material EOC) that month.
In each of these cases, the “EOC ACWP substitution” was temporary, and the work resumed the next period as planned, using the originally planned Element of Cost. The key here is that in each case, the work was performed, and so it was earned; as it should have been. The only difference was that a different EOC was used to accomplish the work – a simple Cost Variance. While it is certainly true that each WP (and PP) should be planned and WPs earned using a single EOC, the misinterpretation here was that every EOC then is a Work package and they are not. In other words, temporarily using a different Engineer category than planned, or using contract support instead of internal labor, or substituting a purchased material item instead of fabricating internally, etc. simply represents a Cost Variances, and should not be cited as a violation of the EVMS Guidelines.
The “consistency” required by the Guideline and the sub-question is that the EOC actually used was expended in the same period in which the work was completed and the Earned Value claimed (i.e. consistent with the BCWP). The variance analysis would show BCWS, BCWP, and ACWP at the CA level with the EOC details at lower levels.
Now for the big “HOWEVER”!
If the switch in use of the alternate EOC is short term, then the differences should be addressed as a Cost Variance (which could be higher or lower than with the planned EOC); HOWEVER, if the change is expected to be permanent or long term, then the CAM should replan the remainder of the work package using the new EOC, and the EAC should be updated, as well, to reflect the new anticipated total cost using that revised EOC.
Note: Some contractors have what is called a “gray badge” environment, whereby a subcontractor charges their labor directly into the Prime contractor’s labor system. Under this arrangement, for this subcontractor, there would be no difference in EOC if the subcontractor performed the work instead of the prime contractor.
Humphreys & Associates is available for consulting and information on this topic. Give us a call!
Planning and Managing EVM by Elements of Cost (EOC) – Use a New EOC – Part 3 Read Post »
EIA 748-D Released – Change Notes
Portions extracted from the EIA-748-D © SAE International (with permission).
Are you aware that a revision to the Society of Automotive Engineers (SAE) / Electronics Industry Alliance (EIA) Standard 748 Earned Value Management Systems, has been released? The new revision is SAE / EIA 748-D. Officials have been discussing the changes at recent industry conferences.
Sections 2.1-2.5 – No Changes to EVMS Guidelines
No changes have been made to the 32 EVMS Guidelines in Sections 2.1-2.5 of the standard. The changes are primarily clarifications of the existing text:
Section 1 – Additional 4th Note
Section 1 “Scope of EVMS” previously “Introduction” in 748-C now has an additional 4th Note:
“Note 4: There are occasions where it is beneficial for complementary systems or methodologies (e.g., Enterprise/ Manufacturing Resource Planning, Agile Software Development, Theory of Constraints) to interface with the EVM System. These complementary systems or methodologies can be used to deliver functionality and value to the customer while EVM provides a standardized method for measuring progress and reporting across the contract. The EVMS documentation should describe the interface content as well as the recurring control process to maintain data conformance and system compliance.” © SAE
Section 2.6 – Six Additional Terms
Section 2.6 “Common Terminology” includes six additional terms:
ACTIVITY OR TASK: An element of work with an expected duration in the network schedule that is performed during the course of a project. Activities generally have expected resource requirements used to determine the budget for the work effort. One or more activities may relate to a work package.
AUTHORIZED UNPRICED WORK (AUW): A contract scope change which has been directed by the customer’s contracting officer but has not yet been fully negotiated/definitized. It includes a value, excluding fee or profit, typically associated with the authorized, unpriced change order.
ELEMENT OF COST (EOC): The categories of cost such as labor, material, subcontractor, and other direct costs as defined by company accounting practices.
OVER TARGET SCHEDULE (OTS): A replanned schedule baseline that extends beyond contract milestone dates, delivery dates, or completion date. An OTS is usually accompanied by an increase in budgets resulting in a corresponding Over Target Baseline (OTB). It typically requires customer approval to implement.
RISK AND OPPORTUNITY (R&O): An uncertain future event or situation that could impact the ability to achieve overall project requirements within defined cost, schedule, and technical objectives. Risk has two components: (1) the probability (or likelihood) of a particular outcome and (2) the consequences (or impact) of that outcome. The consequences of risks are typically thought of as negative that may need to be mitigated to minimize the impact to the project. A risk event with positive consequences is referred to as an opportunity that may be captured as a benefit to the project.
SUMMARY LEVEL PLANNING PACKAGE (SLPP): An aggregation of far-term work efforts (scope, schedule, and budget) that are not able to be identified at the control account level but can be distributed to reporting level WBS elements.
Section 2.6 – Term Changes
Section 2.6 “Common Terminology” includes changes/clarifications to existing terms:
ESTIMATE AT COMPLETION (EAC): The current estimated total cost for authorized project work. It equals the cumulative to date Actual Cost of Work Performed (ACWP) plus the estimated costs to complete (Estimate to Complete or ETC) the authorized work remaining.
LEVEL OF EFFORT (LOE): Support type activities that lack measurable output or product that cannot be discretely planned or objectively measured in a practical manner. LOE automatically earns performance with the passage of time, an earned value technique.
MANAGEMENT RESERVE (MR): An amount of the total budget set aside for unplanned, in scope effort that may arise during the course of the project which cannot be identified in advance and is used to handle execution risks. Management reserve budget should be commensurate with the level of project risk. It is not part of the Performance Measurement Baseline (PMB).
OVER-TARGET BASELINE (OTB): A Performance Measurement Baseline (PMB) that exceeds the Contract Budget Base (CBB). It is implemented to produce a realistic schedule and budget plan for the project’s remaining work. It typically requires customer approval to implement.
Section 2.7 – 3 Additional References
Section 2.7 “List of Suggested References” has been updated to include 3 additional references. The complete list is below:
– NDIA IPMD EVMS Intent Guide
– NDIA IPMD IBR Guide
– NDIA IPMD Surveillance Guide
– NDIA IPMD EVMS Acceptance Guide
– NDIA IPMD EVMS Application Guide
– NDIA IPMD Planning and Scheduling Excellence Guide (PASEG)
– NDIA IPMD Industry Practice Guide for Agile on Earned Value Management Programs (New)
– NDIA IPMD Master Definitions List for IPMD Guides (New)
– NDIA IPMD Earned Value Management System Guideline Scalability Guide (New)
Sections 3 thru 5
In Section 3.2.1 WBS Dictionary, discussion regarding segregation by WBS element for direct costs has been removed.
In Section 3.3.1 Control Accounts, discussion regarding guidance that a Control Account shall not span multiple WBS elements has been removed.
In Section 3.3.1, a new figure, Figure 1 – Establishing Control Accounts was added.
In Section 3.4.3 Subcontract/Procurement Schedules, the phrase “high risk” has been removed.
In Section 3.8.2 Cost Performance, The Labor Rate and Efficiency variance calculations were corrected. The corrected equations are below.
• Labor Rate Variance Calculation = Actual Hours x (Earned Rate – Actual Rate)
• Efficiency Variance Calculation = Earned Rate x (Earned Hours – Actual hours)
In Section 3.8.2 Cost Performance, the acronym “EAC” has been replaced with “ETC”.
In Section 3.10.2 Authorized Changes, discussion regarding allowable changes for optimum utility has been removed.
In Section 4 System Documentation, the term “GEIA” has been replaced with “SAE”.
In Section 5.1, Evaluation Process, the term “officer” has been replaced with “authority”.
In summary, EIA 748-D has added/modified a few items for clarification but does not change any of the implementation, reporting, surveillance, or enforcement aspects of Earned Value Management Systems.
Purchase a copy of the standard here: https://www.sae.org/standards/content/eia748d/
EIA 748-D Released – Change Notes Read Post »
Planning and Managing EVM by Elements of Cost (EOC) – Over-Application of EOCs – Part 2
<< Review Part 1
In part one of our series on Elements of Cost (EOC), we explained what EOCs are and gave an analogy of how EOCs would relate to building a patio. We also reviewed how EOCs can be “over thought” and emphasized the importance of properly applying indirect cost rates. This post is going to be focused on the Over-Application of EOCs.
Over-Application of EOCs
During some government reviews, the teams issued Corrective Action Requests (CARs) citing multiple examples of ACWP occurring on “zero-budgeted” Work Packages within Control Accounts. On the surface, this sounds pretty serious, but there were several “over-applications” in play here.
- First, the review was being performed at (and in some cases below) the Work Package (WP) level, when the intent of the Guidelines has always been for variance analysis to be performed at the Control Account (CA) Level;
- Second, the CAR assumption was that a charge against an Element Of Cost (EOC) equals a charge against a “zero-budgeted WP”.
For the first point we’ll look at Guideline 22 in the EVM Standard 748:
GL 22. At least on a monthly basis, generate the following information at the Control Account and other levels as necessary for management control using actual cost data from, or reconcilable with, the accounting system:
1) Comparison of the amount of planned budget and the amount of budget earned for work accomplished. This comparison provides the schedule variance.
2) Comparison of the amount of the budget earned and the actual direct costs for the same work. This comparison provides the cost variance.
Even the government’s sub-question e. under GL 22 reiterates this requirement:
e. Are the following elements for measuring performance available at the levels selected for control and analysis (at a minimum at the control account level):
1) Budgeted Cost for Work Scheduled (BCWS)?
2) Budgeted Cost for Work Performed (BCWP)?
3) Actual Cost of Work Performed (ACWP)?
While the intent of the words “and other levels” and “at a minimum” was to ensure that contractors did not only perform analysis at some higher, summary level, the government’s choice of those sub-question words also opens up the application of the analysis at lower levels. Be that as it may, the over-application still exists where it should not. Variance Analysis is supposed to be at the CA level and rolled up to higher levels for analysis. The bottom line for each of the CARs written is that BCWS, BCWP, and ACWP existed at the Control Account level, and the EOC visibility was available for variance analysis explanations at the lower levels in the contractors’ systems.
For the second point, let’s look at all the EVM Standard 748 Guidelines, specifically Guideline 16.
There is no Guideline that specifically requires BCWP to be claimed the exact same way BCWS was planned; however, it is intuitive that this has to be true in order for cumulative values for BCWP and BCWS to equal BAC so that the work can be considered complete. [While the government’s sub-question b. under Guideline 22 expects BCWP to be calculated “consistent with the way the work is planned”, GL 22 itself (above) is silent on that inferred expectation.] The Guideline 16 and its sub-question b. also require consistency of the direct costs:
GL 16. Record direct costs in a manner consistent with the budgets in a formal system controlled by the general books of account.
- Are elements of direct cost (labor, material, subcontractor, and other direct costs) accumulated within control accounts in a manner consistent with budgets using recognized acceptable costing techniques and controlled by the general books of account?
In the examples noted for the CAR referenced above, the work package task was a specific Element Of Cost (EOC) and was planned and completed in the same period, but no ACWP was accumulated for that specific EOC because the work was accomplished using another resource that fell into another EOC category. When the team looked at that EOC containing the ACWP, they interpreted the finding as a “zero-budgeted Work Package” with ACWP against it. [They also cited the original Work Package itself for having BCWP with no ACWP for the element of cost that was planned and earned.]
Humphreys & Associates is available for consulting and information on this topic. Give us a call!
Planning and Managing EVM by Elements of Cost (EOC) – Over-Application of EOCs – Part 2 Read Post »
Planning and Managing EVM by Elements of Cost (EOC) Example: Building a Backyard Patio – Part 1
What are “Elements of Cost”?
Labor, Materials, Subcontracts, Other Direct Costs, and their Indirect Costs (Overhead including General and Administrative —G&A) are the typical building blocks for any project: personal projects and projects we manage for the customers we support. These items are also what the Earned Value Management System (EVMS) Guidelines call elements of cost (or EOCs). So, when the Guidelines call for us to plan and manage by EOC, it really should not cause us any undue anxiety – it is just the natural way to manage any project.
Example: Outdoor Backyard Patio
Let’s use a simple home project example of building an outdoor backyard patio: What do you have to do to determine how much it will cost for this Backyard Patio Project (BPP if you like acronyms)? Generally, you look at such things as:
- How much concrete; lumber for decking; nails, screws, bolts, washers, and other hardware, etc.; and weather-coating and paints/stains you will need (Material Element of Cost – EOC).
- Work you cannot do by yourself: electricity for lights and power, and natural gas for the Barbecue/fireplace (Subcontract EOC).
- Work you will do yourself (Labor EOC).
- Costs unique to this project’s completion, such as: Home Owners Association permits, building code permits, local excavation application fee, etc. (Other Direct Cost EOC).
- Costs incurred that do not necessarily go into the final product, such as: cleaning supplies, brooms, solvents, turpentine, weather tarpaulins, lighting and electricity, etc. (Indirect Costs/Overheads).
Unfortunately, when operating under the EVM requirement, often managers tend to overthink, and sometimes over apply the management of EOCs. Let’s look at the overthinking part first.
Overthinking EOCs
Guideline 9 of the EIA Standard 748 (Revision D) for EVM Systems requires:
- Establish budgets for authorized work with identification of significant cost elements (labor, material, etc.) as needed for internal management and for control of subcontractors.
Some might propose: “I’ll have one Work Package for the Control Account with all the EOCs in it, and I’ll be okay.” That might meet the intent of that first part of the guideline, but would probably fail the requirement that says “as needed for internal management and control of subcontractors.” For example, what EV technique would you use for a “work package” that had labor, material, and subcontract work in it? The labor occurs as the work is performed, the material might be earned at the point of receipt on the dock, and the subcontract might earn value with the receipt of an Integrated Program Management Data and Analysis Report (IPMDAR) dataset at the end of a month. Since the Control Account (CA) has one total dollar budget, the “identification of significant cost elements” has to occur at the Work Package (WP) and Planning Package (PP) level within the CA, which requires each WP and PP to be identified as one of the EOCs mentioned above.
For Instance
In our example, if we lumped concrete and lumber into one “Material WP” and we incurred a serious overrun in material, how would we identify what caused the overrun: the concrete pour or the lumber portion? These are different categories of material that would “earn value” (be accomplished) in different ways and at different times. In order to determine the “guilty party” in the overrun, we should also have separate WPs for the different significant material categories. Some might call these major, or high value, or critical material items, which should be tracked separately.
On the other hand, for the lower-value materials, it may not be significant enough to management to know that a variance might have been caused by a 1-cent washer or a pint of deck stain. Consequently, a grouping of these low-value material items may be all that is required for visibility. Conversely, Management might actually want to break out categories such as, separating the paints/stains, and weather-coating from the nuts, bolts, washers and other hardware, since they are different categories of low-value material that could also earn value differently.
Indirect Cost Rates Must be Applied Properly
For Indirect Costs, some contractors put the burden of planning and managing these overhead costs on the CAMs, while others apply the indirect rates at a summary level of the Work Breakdown Structure (WBS) or organizational structure. Regardless of how a particular contractor does it, the indirect cost rates must be applied properly to the various direct elements of cost:
- Material handling charges applied to material items
- Indirect Labor rates applied to the direct labor hours
- Subcontract overhead applied to the subcontract direct costs
- ODC overheads charged to the ODCs identified.
Applying and managing overheads at the CA level would entail hundreds of applications across the number of Control Accounts on a project, but applying these at a summary level would require only a handful of Overhead lines in reports. Doing so would significantly reduce the number of possible errors in application – which is why many contractors do not require CAMs to “manage” overheads in their Control Accounts. [Our BPP example does not have the above types of Indirect Costs that are related to specific Direct Costs, but it does have its own specific Overheads related to the labor to build the Patio.]
Humphreys & Associates is available for earned value training and consulting. Give us a call!
Earned Value: Fun with Numbers or Real Management Data?
What Are Earned Value Basics?
We used a quick quiz with some helpful links to give you an opportunity to test your basic understanding of an EVM graph from a real EVMS Program. We go into detail about each concept displayed in the graph and our overall analysis of the project based shown in the graph.
Earned Value: Fun with Numbers or Real Management Data? Part 1
In Part 1 we reviewed where you could find more information about EVM Implementation and Basic Concepts of Earned Value on our site. We also included a review quiz.
- EVM Implementations
- EVM Graph Quiz Testing Basic Earned Value Terms
Earned Value: Fun with Numbers or Real Management Data – Answers (part 2)
In Part 2 we provided the answers to the EVM Quiz and provided detailed definitions and descriptions for each of the quiz terms.
- EVM Quiz Answers
- Management Reserve
- Schedule Variance
- Budget At Completion
- Contract Budget Base/Contract Target Cost
- Budgeted Cost for Work Scheduled
- Schedule Slip
- Variance At Completion
- Estimate At Completion
- Actual Cost of Work Performed
- Estimate To Complete
- Cost Variance
- Program Overrun
- Time Now
- Budgeted Cost for Work Performed
- Forecasted Program Schedule Slip
- Estimated Completion Date
- Discussion of the displayed data
Earned Value: Fun with Numbers or Real Management Data? Read Post »