Why Expert Planning and Scheduling Resources Matter
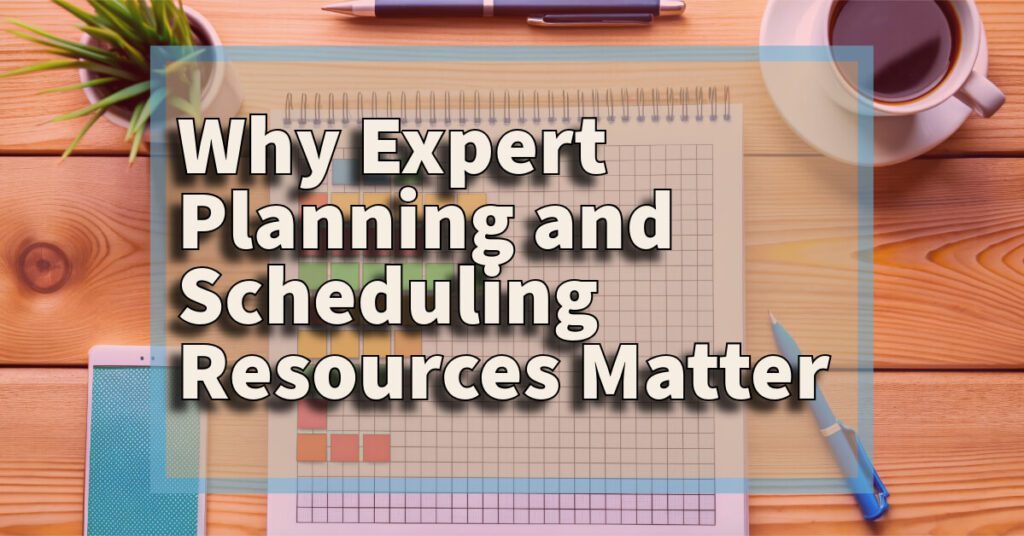
At Humphreys & Associates, conducting a requirements analysis of a contractor’s current integrated program management or earned value management (EVM) practices is one of our most frequently requested services. We are also the “911” call that contractors make when they need to quickly solve an Earned Value Management System (EVMS) compliance issue. When we reviewed our findings and observations from the past year, a common issue that stood out was the lack of sufficient scheduling expertise.
As many project managers, project control teams, and control account managers (CAMs) recognize, a well-planned and constructed schedule provides a model of when work will be performed and what resources are required to perform the work. A well-planned and constructed schedule must be realistic, challenging, and achievable, and be based on a well-thought-out execution plan. It also provides an overall view of performance to date and displays the forecast schedule for remaining work.
Equally important, a well-planned and constructed schedule becomes the principal communication tool for the project team. It shows when major events are planned to occur as well as the completion dates for all activities preceding them along with the resources required to support the scheduled activities. Ensuring resources are available to execute the schedule and performing a schedule risk assessment (SRA) also help to ensure the schedule is realistic and achievable.
A well-constructed and maintained schedule facilitates project performance analysis and to assess how changes affect project objectives. It provides an early warning of potential issues for effective and timely management corrective action.
Scheduling Best Practice Guidance
Several industry and government documents discuss scheduling principles and best practices for major projects within the US Federal Government acquisition environment. Two frequently referenced documents include the National Defense Industrial Association (NDIA) Integrated Program Management Division (IPMD) Planning and Scheduling Excellence Guide (PASEG) and the Government Accountability Office (GAO) Schedule Assessment Guide: Best Practices for Project Schedules. These guides define what is considered a “good schedule.”
Some of our recent blogs have highlighted the nuances of producing a well-constructed integrated master schedule (IMS) that reflects the work to be performed and communicates that plan to everyone on the project. This includes Improving Integrated Master Schedule (IMS) Task Duration Estimates, Including Level of Effort (LOE) in the Integrated Master Schedule (IMS), and Establishing Milestones in the Integrated Master Schedule (IMS) Appropriately.
What’s the Problem?
A project’s integrated master schedule (IMS) is only as good as the team that built it and the master planner/scheduler that assembled it. Scheduling is a combination of art, science, and discipline. A master planner/scheduler ensures there is clear communication on what needs to be done when along with defining how to handle day-to-day issues. They translate all of the inputs and organize the puzzle pieces into a coherent road map for the entire project team to understand and to use. The experience and schedule maturity level of the planner/scheduler is a key ingredient.
When our earned value consultants identify issues with the construction or content of an IMS, a common discovery was that the client’s scheduling team needed help with basic scheduling techniques.
Here is a sample of common findings in the past year where the client’s scheduling team and/or the master planner/scheduler, could not provide satisfactory answers to schedules under review. They needed more mature scheduling expertise.
- Invalid critical path. The team could not display the critical path from “time now” through the end of the project. When asked to push an activity on the critical path by 300 days, they could not explain why the successor activities and end date did not move by the same 300 days.
- Lacked awareness of the scope of work. During scheduling reviews, we ask the team how they know all requirements have been accounted for in the IMS. A common response is they rely on the individual CAMs to identify their scope of work requirements. In many instances, the entire team did not read the required contractual documents such as the statement of work, systems engineering management plan, CDRL requirements (DIDs), or the program management plan that affects them. Some did not understand the work breakdown structure (WBS) or the purpose of the WBS and how important it is for integration with the cost tool.
- Improper baseline management. We have found that team members and/or the planner/scheduler simply insert the new baseline dates instead of updating the baseline task by task. A separate baseline IMS file should be maintained monthly and approved baseline changes should be incorporated into the revised baseline IMS, and then updated in the current IMS file.
- Change management was lacking. The team could not explain or identify the changes incorporated into the IMS. Many planners/schedulers do not realize they are the “historians” for the project. The planner/scheduler should understand the impact of every change order or delay on the schedule. A big part of this is documenting who (customer or project team) caused the delay or whether it was caused by both parties. All changes during a reporting period should be assessed for delays and documented in the monthly schedule status report. If a change order causes a delay, it must be documented in the monthly report. Why is this important? Project records should document what and who caused the delay.
- Ah-hoc integration of major procurement items and subcontract management. Without a documented approach for how material is incorporated into the IMS, it can be a daunting task to identify impacts when delays occur. The planner/scheduler should understand how purchase order line items are structured and should include tasks for each within the IMS. For subcontracts that have EVM and IMS requirements, it is important that the subcontractor’s schedule is modeled within the IMS at the appropriate level of detail. As a result, delays can be clearly demonstrated.
Meeting the Challenge
Planning and scheduling are critical to the success of all projects. Having a strategy to develop competent planners/schedulers ensures you have the resources with the necessary creative talent, skill set, discipline, and communication skills needed to produce quality schedules. Strategies to help scheduling personnel to improve their level of expertise include:
- Establishing a corporate training program for planners/schedulers. This could be an internal set of courses or public training courses could be leveraged as part of that training program. The goal is to ensure the planners/schedulers and other project team members have the knowledge base to successfully develop and maintain schedules for your business environment. H&A offers a range of project scheduling training workshops that can help schedulers to implement industry best practices in an EVM environment tailored to common tools such as Microsoft Project (MSP) or Primavera P6. These workshops include hands-on exercises that help the students learn how to apply what they are learning in a real-world environment.
- Hands-on mentoring. Our clients are often aware of the limitations of their scheduling personnel particularly when it comes to incorporating more advanced scheduling techniques such as SRAs. H&A provides planning/scheduling and risk management subject matter experts (SMEs) to help clients establish a repeatable process as well as to conduct a series of hands-on workshops with the client’s project planners/schedulers. These workshops help them to gain the experience they need to routinely conduct SRAs, to use the schedule and risk tool outputs wisely, and to use that information to produce more realistic schedules.
- Producing schedule procedures or guidance to ensure the scheduling team is following a consistent repeatable process. Consistency helps to ensure that project personnel have the necessary knowledge base to develop and maintain an IMS in an EVM environment. This includes integrating the IMS with the cost tool as well as other systems such as an M/ERP system in production environments or integrating subcontractor scheduling data.
In situations where it is necessary to bring in outside scheduling personnel to supplement a project team, it is important to verify the scheduler’s skill set and level of expertise in an EVM environment. Just because someone states they know how to use a given scheduling tool it doesn’t mean they know how to plan and schedule. The company you choose to support you matters.
H&A routinely provides expert scheduling staff augmentation services for clients that need to fill short or long term planning/scheduling resource needs. Some clients need surge support to develop a baseline schedule for a new contract award and/or to get them through the initial work definition and planning process. H&A planners/schedulers frequently help project teams to establish and execute the weekly or monthly business rhythm until the client’s project control team is ready to take over.
Another common request is for H&A master planner/scheduler hands-on expertise to resolve a variety of schedule issues. H&A planners/schedulers often provide one-on-one mentoring to client project personnel to work through perceived or identified deficiencies. This can range from helping to configure the scheduling tool appropriately, teaching how to use the software effectively, and showing how to fix schedule construction issues as well as establishing a disciplined process that improves the quality of the schedule.
We know the planning/scheduling resources we provide to clients have the necessary level of planning, scheduling, and EVM expertise. The people we hire are required to complete a scheduling exam to verify their knowledge level; they are also known resources that other H&A consultants have worked with.
Interested in learning more?
Whether you need training, hands-on mentoring, or staff augmentation, H&A has the support services and solutions to fit your needs. Call us today at (714) 685-1730 to get started.
Why Expert Planning and Scheduling Resources Matter Read Post »